Eleven ways to improve your warehouse profitability with and without technology
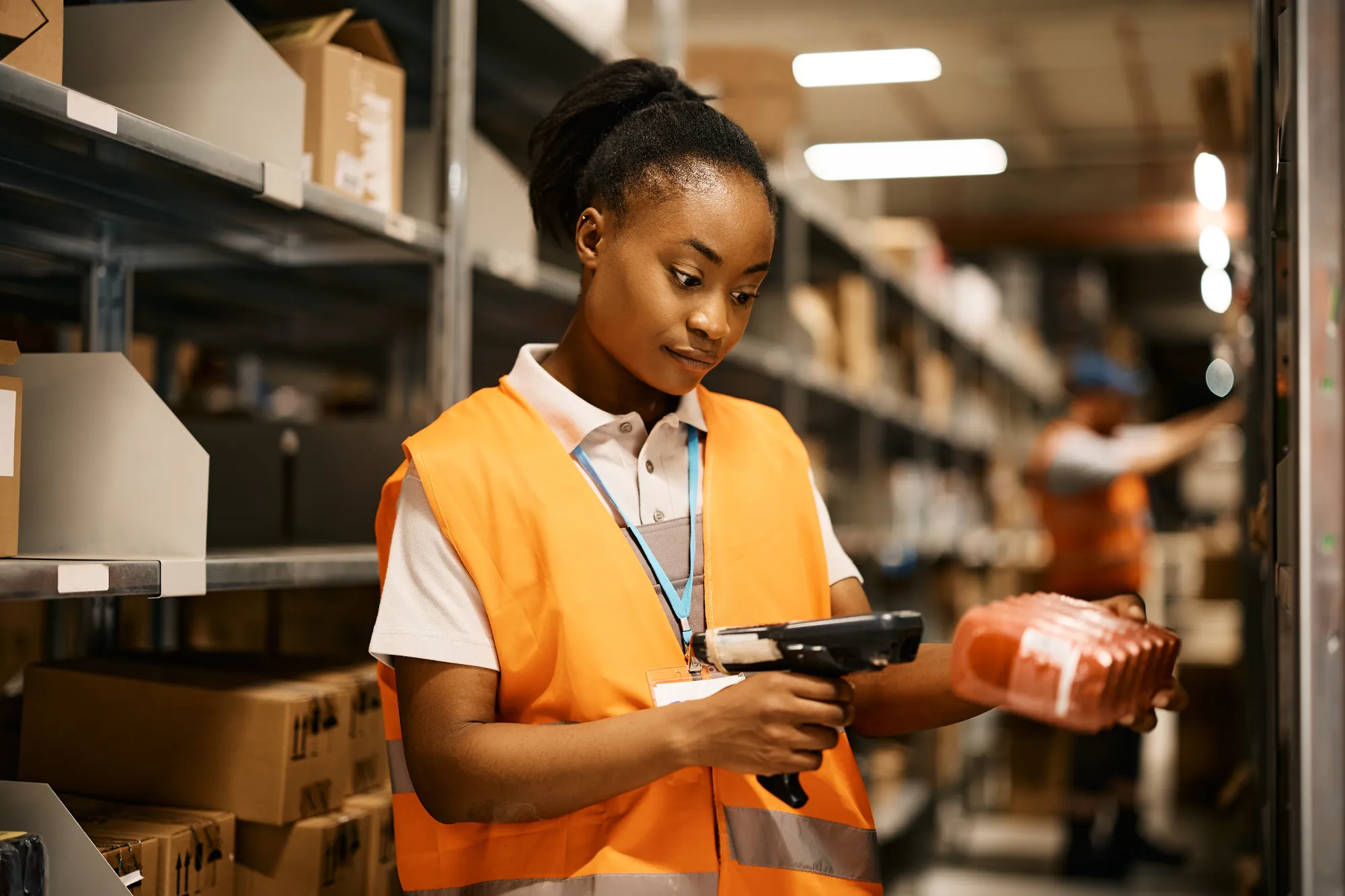
The warehousing landscape is evolving, and the demand for efficient and cost-effective operations is growing. However, improving warehouse profitability is not just about cutting costs. To succeed in a competitive and continuously evolving market, companies across the supply chain must enhance productivity and utilize advanced technologies.
Read this article to discover 11 ways of enhancing your warehouse’s profits, with a specific focus on technology, software solutions, and optimization measures.
Reasons to invest in optimizing your warehouse
Improving profitability is a business challenge that requires strategic planning and methodical execution, but if you are successful, it will help your warehouse maintain a healthy bottom line and stay ahead of the competition.
With innovative technologies and optimized processes, you can improve your facility’s performance in a number of ways.
Optimizing warehouse operations
Optimization is the foundation of improving warehouse profitability. It involves refining processes and systems to maximize efficiency and reduce costs.
1. Warehouse layout design
Effective warehouse layouts minimize workers’ travel time, streamline workflows, and maximize available space. By strategically placing high-turnover goods closer to shipping areas, warehouses can reduce item collection times and increase overall efficiency.
Implementing vertical storage solutions and using the correct shelving systems for your inventory can maximize space utilization and reduce retrieval times. Creating designated zones for different functions (such as receiving, packing, and shipping) will minimize crossover and improve process flow, reducing bottlenecks and increasing throughput.
Designing workstations that minimize physical strain helps reduce worker fatigue and improve their productivity. Ergonomically sound workplaces also lead to fewer injuries and lower absentee rates.
Another noteworthy thing to consider is an adaptable warehouse layout. This will allow for changes based on seasonal demand or product line shifts, ensuring that the warehouse always operates at peak efficiency.
2. Labor management
Optimized labor management allows businesses across industries to improve operational efficiency. Both small businesses and companies with multiple warehouses in different locations can easily implement labor management methods to manage their workforce effectively.
For example, with easily understandable and transparent performance metrics (key performance indicators - KPIs), employees know what is expected of them, and employers can identify each warehouse worker’s strengths and weaknesses.
These metrics can also be used to reward employees for exceptional performance. Creating motivation programs often results in higher productivity, elevated employee satisfaction, and lower turnover rates. When combined with regular performance reviews, these metrics help ensure employees meet targets and determine their training needs.
Cross-training employees on various tasks and implementing continuous training programs will ensure they are well-versed in the technologies and processes used in the warehouse, leading to improved productivity and fewer picking errors. Implementing flexible work schedules can help manage peak times more efficiently.
Many modern warehouse management systems (WMS) include tools linked to labor management. Leveraging WMS features such as directed putaway/picking and batch picking go a long way in improving warehouse workers' UPH (units per hour) and invariable efficiency as a whole. Dedicated labor management software can also greatly benefit companies in the logistics and transportation industry by helping balance workloads and reduce warehouse downtime.
Companies in transportation and logistics can also benefit from leveraging external partnerships to access expert talent with recruitment process outsourcing and managed services. Specialized workforce solutions providers like Maxima Consulting empower clients to effectively address skills shortages in technology and engineering roles while delivering significant cost optimizations.
3. Standardized processes
Process standardization guarantees that tasks are performed steadily and competently. By creating standard operating procedures (SOPs) and regularly reviewing them, warehousing companies can identify areas for improvement and ensure best practices are followed, even across multiple warehouses.
SOPs can also eliminate waste in processes, resulting in more efficient operations and increased profitability.
Remember that all standardized processes must be well-documented. Detailed documentation helps maintain consistency and can be used as a training resource for new hires.
Leveraging warehouse software tools
Modernizing legacy IT solutions and implementing state-of-the-art systems, software solutions, and digital tools is critical to improving warehouse operations and efficiency. Transportation management, warehouse management, and inventory management software enable companies to manage business operations effectively and make more informed decisions.
4. Order management systems (OMS)
Order Management Systems play a crucial role in managing a wide range of aspects in an omnichannel business, including:
- order processing,
- routing,
- inventory management,
- forecasting,
- purchasing.
Particularly, OMS is an ideal choice for omnichannel and multi-warehouse businesses, as it can intelligently determine whether shipping is from the nearest and the most cost-effective facility.
5. Inventory management systems (IMS) and supplementary tools
Proper inventory management reduces holding costs and minimizes stockouts. Utilizing barcode scanning or RFID technology enables more reliable inventory tracking, which speeds up both inbound and outbound processes.
By facilitating regular cycle counting, such technologies can significantly reduce errors in inventory accuracy without the disruption of shutting down all operations for an annual physical count. This ongoing approach fosters real-time inventory control and minimizes discrepancies.
Implementing a just-in-time (JIT) inventory system ensures that products arrive only as needed, thereby reducing excess stock and associated expenses. Such systems also allow for segmenting inventory based on turnover rates (high, medium, low) and facilitate focusing resources on managing high-value or high-movement items.
By utilizing demand forecasting tools, you can accurately predict future inventory needs, reduce excess stock, and ensure timely replenishment. If you have multiple warehouses that are not too far apart, you can assign different functions to each one.
For example, one could be the hot storage tasked with the distribution of fast-moving items, and the others could become the cold storage facilities with reserve stock ready to be shipped to the hot storage when needed.
6. Transportation management systems (TMS)
Transportation management systems streamline the process of transporting goods by optimizing routes, managing carriers, and consolidating shipments. As a result, a TMS can reduce shipping costs, improve delivery times, and significantly enhance supply chain efficiency.
Transportation management software utilizes advanced algorithms to calculate the most efficient routes and the best locations for layovers, reducing fuel consumption, travel time, and labor costs.
Moreover, such systems often allow for more effective coordination of multiple third-party carriers, ensuring the best rates and service levels.
Enhanced visibility and tracking capabilities of TMS solutions offer real-time updates on shipment status. This improves customer satisfaction, as customers can track their packages on their computers or mobile devices, and enhances planning capabilities for warehouses and other supply chain partners.
7. Warehouse management systems (WMS)
A warehouse management system (WMS) is a software solution that integrates various warehouse management functions, including inventory management, order processing, and shipping processes.
For example, warehouse management software can be used for tracking inventory levels and locations within the warehouse in real time to ensure quick and accurate order picking. The best WMS software is also equipped with robust analytics features that use real-time data to help companies optimize operations, reduce errors, and increase throughput.
Most modern warehouse management systems integrate seamlessly with other software systems, including inventory management software (IMS), transportation management software (TMS), enterprise resource planning (ERP), and customer relationship management (CRM) solutions.
Utilizing other technology solutions
Contemporary logistics software is increasingly influenced by the latest technology trends, including recent developments in cloud platforms, automation, the Internet of Things (IoT), and artificial intelligence/machine learning (AI/ML).
Because of these technologies, the broad transportation industry is changing, and warehouses must also transform or risk increased competition from more technology-versed challengers.
8. Automation and robotics
Automation technologies, such as robotic picking systems or automated storage and retrieval systems, are becoming increasingly popular among the warehousing industry leaders because the ability to automate various processes increases warehouse productivity.
Automated storage and retrieval systems (AS/RS) maximize storage density and enable quick, accurate retrieval of items, improving the time it takes to fulfill orders and reducing space requirements.
Automated Guided Vehicles (AGVs) autonomously transport goods within a warehouse, which reduces picking errors, decreases the need for human labor, streamlines the movement of goods, and consequently minimizes the time needed to fulfill an order.
Generally speaking, automation-based systems pick items faster and track inventory more accurately than human workers, so they significantly accelerate the order fulfillment process while simultaneously reducing warehouse labor costs.
9. Internet of Things (IoT)
IoT devices, such as smart sensors and RFID tags, are used in warehouse operations to enable real-time visibility of your current inventory. These devices track the movement and condition of goods, alerting you to potential issues and greatly enhancing the inventory management process.
Smart devices can monitor environmental conditions such as temperature and humidity, ensuring optimal storage conditions for various items by alerting your staff if any deviations occur.
IoT equipment can also predict potential failures before they occur, allowing for preventive maintenance and reducing downtime.
10. Artificial intelligence and machine learning (AI/ML)
A broad scope of AI technologies, including machine learning algorithms and predictive analytics, has already been utilized to transform the entire supply chain management. By analyzing historical and real-time data, AI systems can help companies forecast demand and optimize inventory levels in time.
Moreover, machine learning algorithms are used to analyze operational data to identify inefficiencies and suggest improvements, continuously optimizing warehouse processes.
AI-based tools can also include multiple beneficial order fulfillment features. For example, algorithms can route various orders to the most appropriate shipping methods and carriers, automatically optimizing delivery times and costs.
11. Cloud platforms
Cloud technology offers increased scalability and availability of various software solutions, including more efficient, dependable, and accessible transport, inventory, and warehouse management systems.
Cloud solutions improve collaboration and decision-making by centralizing data and providing real-time updates. They also make managing warehouses across multiple locations much easier.
The innate scalability of cloud-based solutions is leveraged to easily accommodate changing business needs without the need for significant upfront investments. Furthermore, keeping the warehouse data in the cloud enhances disaster recovery options, ensuring that data is backed up regularly and can be quickly restored in the event of an incident.
In addition, transitioning to cloud-based solutions can reduce IT maintenance costs and the need for on-premises infrastructure, which further lowers operating costs.
Save time and money with a specialized technology partner
While some optimization methods can be achieved with little upfront costs, the integration of technology solutions to improve warehouse profitability is a continuous process that requires specialized, in-demand IT expertise.
However, incorporating advanced warehouse software and hardware solutions and leveraging the latest trends in logistics technology will get the most bang for your buck.
At Maxima Consulting, we are committed to helping you achieve business goals through tailored solutions and expert guidance. Contact us today to learn more about how we can assist you in transforming your warehouse operations.
Frequently asked questions
What is warehouse management optimization?
Warehouse management optimization involves refining processes and systems to maximize fulfillment efficiency and reduce the total cost, ensuring peak operational performance.
How can warehouse software improve business profitability?
Specialized software solutions for warehouses provide real-time data and analytics, streamline processes, and reduce errors, leading to increased efficiency and cost savings.
When to update an existing warehouse management system (WMS)?
Relying on legacy warehouse management software can significantly limit the efficiency of any warehouse. See the article about modernizing warehouse management systems for more information.
What role do IoT devices play in warehouse management?
IoT devices offer real-time visibility into day-to-day operations, track the movement and condition of goods, and enable proactive inventory management.
Can AI technologies really make a difference in a warehouse?
Yes, AI technologies can help in item distribution, forecast demand, optimize inventory levels, and streamline order fulfillment, significantly enhancing warehouse efficiency and profitability.